Key Takeaways
- Smart manufacturing uses Artificial Intelligence (AI), the industrial Internet of Things (IIoT), digital twins, and robotics to solve urgent challenges like labor shortages, rising costs, and quality control.
- Unlike traditional automation, smart manufacturing creates a fully connected ecosystem where data drives real-time decision-making and efficiency.
- Integrating these technologies enables predictive maintenance, sustainable production, and hyper-customized outputs—all while reducing waste.
- Companies like Boeing demonstrate how smart automation and lean practices can significantly enhance production speed, safety, and precision.
- To stay competitive, U.S. manufacturers must invest in digital infrastructure and upskill their workforce to fully unlock the potential of smart manufacturing.
Listen: How smart manufacturing is redefining American industry.
The future of American manufacturing is smart. To compete in an increasingly global marketplace, American manufacturers must adopt intelligent technologies that can anticipate, adjust, and hyper-customize production in real time. These innovations don’t just bring efficiency—they create new value and unlock the potential to re-shore critical industries.
Smart manufacturing isn’t just about automation—it’s about ecosystems. Systems that speak to each other. Data that informs every move. Machines that make production faster, cleaner, and more adaptable. These advancements are arriving just in time. Manufacturers today face pressure to reduce costs, manage labor shortages, meet sustainability goals, and maintain quality—all while remaining globally competitive.
With technologies like AI, the IIoT, digital twins, and robotics, smart manufacturing offers a strategic path forward. And beyond addressing today’s challenges, it positions U.S. industry to bring more manufacturing back home—and build a more resilient, responsive future.
What is smart manufacturing?
Smart manufacturing uses interconnected, intelligent technologies to transform traditional processes. It’s not about automating individual tasks—it’s about enabling entire systems to work together, sharing data, and adapting in real time. In this era, data is the new oil, and the ability to act on it is the key to driving innovation.
This marks a major shift from earlier industrial models. Where traditional factories relied on manual labor or standalone automation, smart factories embrace full digital integration. Machines, sensors, and control systems connect across the operation to drive transparency, agility, and optimization. The result: factories that are predictive, adaptable, and designed for resilience.
Core technologies powering smart manufacturing
AI and machine learning
AI is the brain behind smart manufacturing. It delivers real-time insights, automates complex decisions, and makes efficiency gains that manual processes simply can’t. Predictive maintenance allows systems to detect and address equipment issues before failures happen, reducing downtime and saving money. Computer vision and anomaly detection are used for automated quality control, ensuring consistent standards and reducing waste. AI also optimizes scheduling, inventory, and resource allocation for smoother production flows.
Industrial Internet of Things (IIoT)
The IIoT connects every device on the factory floor. Smart sensors and machines generate constant streams of data, fueling everything from predictive analytics to autonomous decision-making. This enables machine-to-machine communication and responsive control systems. IIoT also enhances energy efficiency, identifies process bottlenecks, and optimizes inventory management—all in real time.
Digital twins
A digital twin is a virtual model of a physical system. It allows manufacturers to simulate and test everything—from new product designs to sustainability strategies—before implementing them. Digital twins are used to optimize factory layouts, improve energy usage, and predict maintenance needs. While the upfront investment can be high, the long-term benefits in efficiency, uptime, and innovation are significant.
Robotics
Today’s robotics go far beyond repetitive tasks. Enhanced by AI, modern robots can handle complex functions with speed and precision. They're helping to close critical labor gaps, especially for hazardous or physically demanding roles. Through adaptive learning, robots continuously improve their performance and can operate collaboratively with human workers. This hybrid workforce is already reshaping production lines across sectors.
Building an interconnected smart manufacturing ecosystem
Digital transformation happens when these technologies work together. By integrating AI, IIoT, digital twins, and robotics, manufacturers can create a truly intelligent ecosystem. Data flows seamlessly across systems, enabling real-time adjustments and predictive decisions.
Cloud and edge computing play key roles in this transformation. Edge devices process data locally at the machine level for rapid action, while cloud platforms provide the big-picture view for strategic analysis and system-wide coordination. Providers like Microsoft Azure and Siemens offer comprehensive platforms that integrate analytics, digital simulation, fault detection, and predictive modeling—all in one suite.
But transformation isn’t only technical—it’s human. Implementing smart manufacturing requires technical expertise, retraining, and often external support. It’s as much an organizational shift as it is a technological one.
The future of smart manufacturing
Smart manufacturing is quickly evolving toward hyper-automation—factories that can monitor, optimize, and even correct themselves with little human input. These highly intelligent systems support more sustainable operations by cutting energy use, minimizing waste, and enabling circular economy practices. The environmental and economic implications are significant.
We’re also approaching a future where humanoid robots may take on more physical labor. As NVIDIA CEO Jensen Huang recently noted, “Humanoid robots are less than five years away from seeing wide use in manufacturing facilities.” This shift prompts deeper questions about the evolving role of humans in industrial work.
As machines take on repetitive tasks, human workers will shift toward roles that prioritize creativity, problem-solving, and innovation. But that requires new skills—data literacy, robotics fluency, and systems thinking. Organizations that invest in training today will be the ones thriving tomorrow.
Case study: Rockwell
Rockwell Automation, in collaboration with Aquent, developed a digital twin of a physical assembly line at their Milwaukee corporate visitor center to showcase the factory of the future to potential customers. Facing challenges in creating real-time 3D graphics and interactive code, Rockwell Automation partnered with Aquent Studios to bring this immersive project to life.
Within a three-month timeframe, Aquent Studios' UX Designers crafted an intuitive touchscreen interface, simplifying complex concepts for visitors of all ages. The team converted CAD assembly line data into real-time mesh data using the Unity game engine, ensuring synchronization between the physical and virtual assembly lines based on live or simulated data. This collaboration effectively bridged the gap between physical manufacturing processes and digital visualization, providing an interactive and educational experience for visitors.
Conclusion
Smart manufacturing is already reshaping how we build, produce, and compete in global markets. For American industry, it offers a chance to address long-standing challenges—while positioning to maintain our global leadership in many industries.
But this revolution requires more than tools. It demands vision, investment, and commitment—from executives and engineers to frontline workers and tech innovators. The manufacturers who act now—adopting interconnected systems, investing in people, and thinking long term—will be the ones who thrive in the next era of American industry.
The future isn’t automated. It’s smart.
Latest.
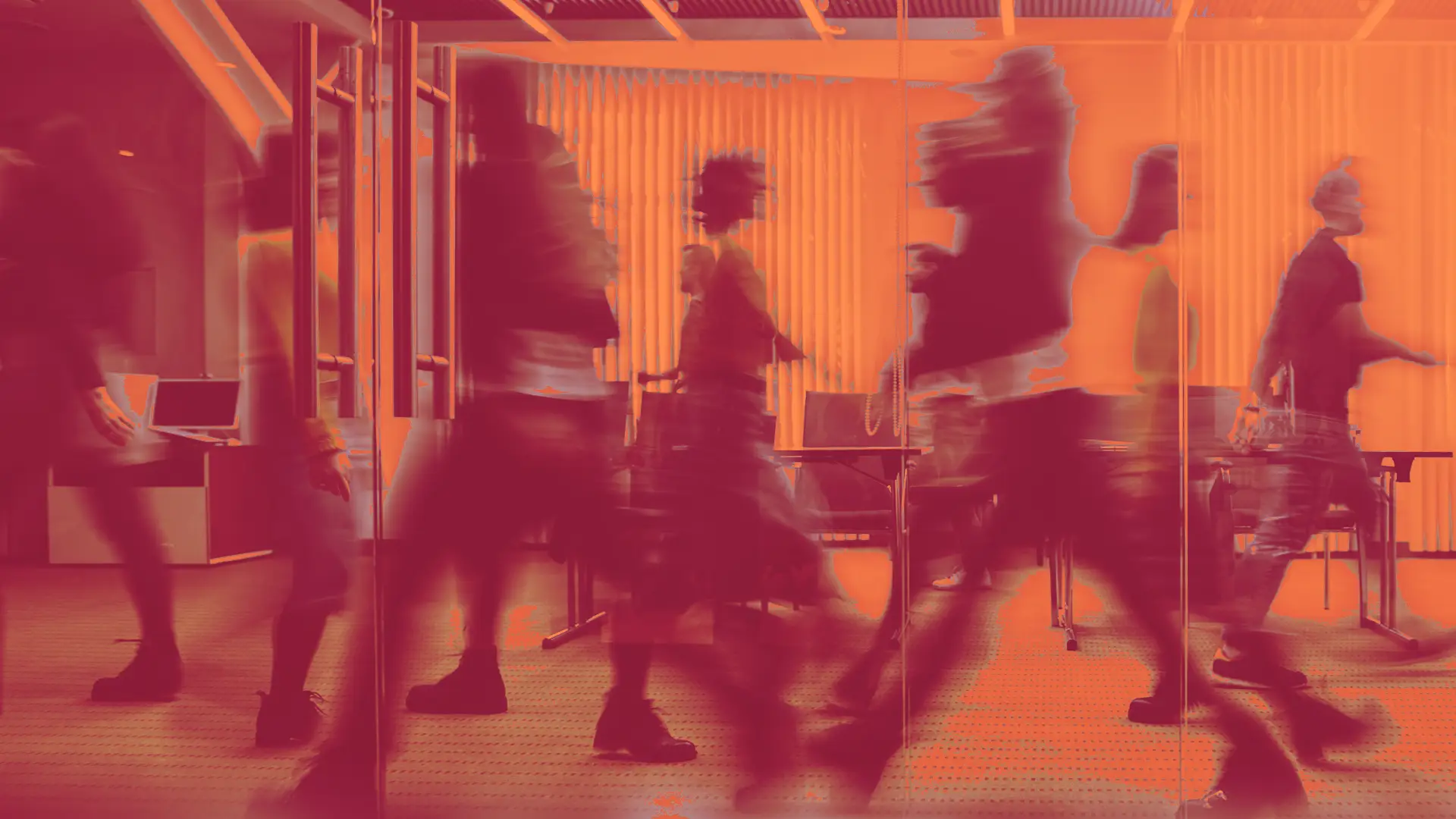
How to keep your team motivated and productive during a RIF.
Diversity, Equity & Inclusion, Leadership & Management, Retention Strategies, Talent Acquisition & Recruitment

New ways leaders can prepare for performance reviews with AI.

Consumers demand better: The ROI of sustainability.
Climate Action, Consulting & Operations, Marketing & Analytics, Sustainability